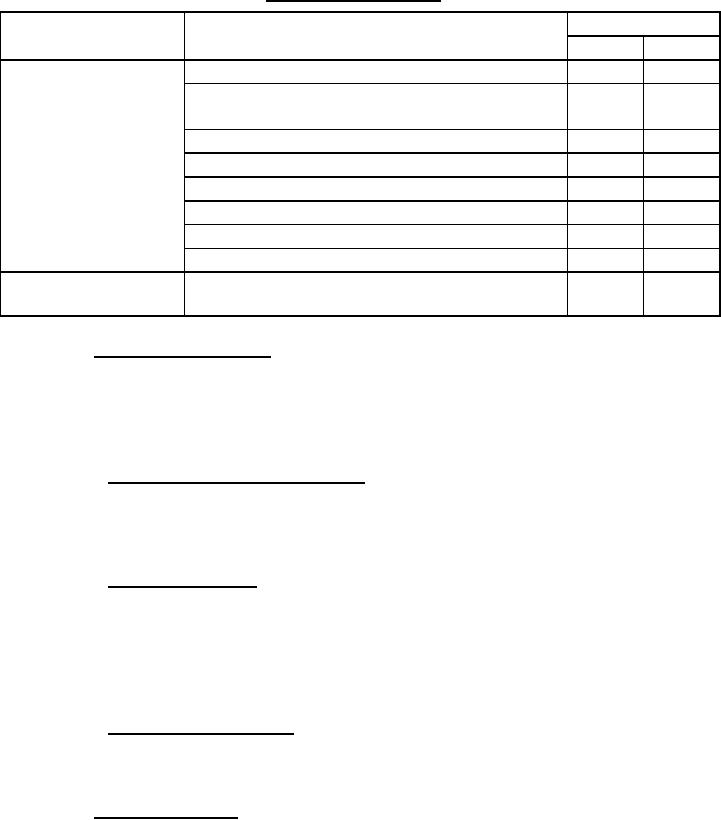
MIL-DTL-43243D
TABLE I. Classification of defects - Continued.
Classification
Examine
Defect
Major
Minor
Welding incomplete or improper type
105
Weld, braze, or silver solder not smooth; any slag
204
or spatter or burn through
Weld, braze, or solder not free of pits or porosity
205
Design construction
Weld, braze, or solder area not clean or free of
206
and workmanship
Lever binds not self-returning
106
Rivet not firmly set or adequately peened
107
Rivet heads not in full contact with adjacent
207
Rivet heads not concentric to rivet holes
208
Missing, incomplete, illegible, incorrect, or not
Identification marking
209
applied as specified
4.3 Conformance inspection. Conformance inspection shall consist of the visual
examination for defects listed in table I as well as the examinations of paragraphs 4.3.1 and 4.3.3.
Unless otherwise specified (see 6.2), the manufacturer, in accordance with MIL-STD-1916, shall
select the type of sampling plan (attribute, variable, or continuous). The sample size shall be
selected in accordance with verification level II of MIL-STD-1916.
4.3.1 Component and material inspection. Components and materials shall be inspected
in accordance with all of the requirements of referenced specifications, drawings, and standards
unless otherwise excluded, amended, modified, or qualified in this specification or applicable
purchase document.
4.3.2 Process examination. Examination shall be made of the following fabrication
processes to establish conformance with specified requirements. Whenever nonconformance is
noted, correction shall be made to the process and all items processed.
a. Heat treatment of spring (see drawing 11-1-240).
b. Cementing of felt pad (see drawing 11-1-176).
4.3.3 Dimensional examination. Inspection shall be made of the separators to determine
compliance with dimensions on drawings specified in 3.2. Any dimension not within specified
tolerances shall be classified a defect.
4.4 Rejection and retest. Any separator failing to meet first article or conformance
inspection requirements shall be cause for rejection of the lot. Separators that have been rejected
may be replaced or repaired and the lot retested using a tightened sample size in accordance with
verification level III of MIL-STD 1916. Prior to retesting, the manufacturer shall provide all
corrective actions taken to correct the defect(s) in writing to the procuring activity. Units
rejected after retest shall not be resubmitted and the lot shall be rejected unless specific approval
is authorized by the procuring activity granting additional corrective actions and testing.
4
For Parts Inquires call Parts Hangar, Inc (727) 493-0744
© Copyright 2015 Integrated Publishing, Inc.
A Service Disabled Veteran Owned Small Business